Analysis some question about seal lose efficacy
A wide range of mechanical seals for pumps, models vary, but there are five leak: (l) the seal between the sleeve and the shaft; (2) ring and the seal between the sleeve; (3) Dynamic and static inter-ring seal ; (4) of the stationary ring and the seal between the stationary ring seat; (5) sealing the seal between the cover and pump body.
1. Static leak test when installed. After mechanical seal installation, generally the static test, observed leakage. If leakage was smaller, and more for the ring seal ring or static problems; leakage is large, then the dynamic and static friction between the ring problem. Leakage in the initial observation to determine the leaking part of the basis, and then manually turning observed, if the leakage were no significant changes in static and dynamic ring seal in question; as Barring significant changes in leakage can be concluded that there is a move problems of static friction ring; such as leakage of the media along the axial jet, the ring seal problems mostly to the surrounding medium leakage from the water spray or leakage of cooling holes, are much more static ring seal failure. In addition, the leak paths may exist, but generally there are differences between primary and secondary, as long as careful observation, familiar with the structure, will be able to judge correctly.
2. When commissioning the leak. After the pump mechanical seal static tests, running high-speed rotation of the centrifugal force, will inhibit the media leak. Therefore, the commissioning of mechanical shaft seal leakage between the exclusion and cover seal failure, basically are due to dynamic and static damage caused by the friction ring. Seal failure caused friction factors are: (l) operation, because the time to cavitation, choke pressure and abnormal, causing large axial force, the dynamic and static ring contact surface separation; (on the installation of mechanical seal When excessive compression, leading to friction face serious wear and tear, scratches; (3) The tight ring seals, spring can not adjust the offset of the axial ring; (4) stationary ring seal is too loose, when the ring axial float, the stationary ring from the stationary ring seat; (5) working media are granular materials, running into friction, testing static and dynamic ring seal face; (6) design selection is wrong, than the seal face pressure is low or relatively high shrinkage and other sealing materials. These phenomena often appear in the test run, and sometimes can be adjusted to eliminate static ring, Block, etc., but most need to re-entry, replace the seal. As the two seal faces caused by loss of lubricant film failure a) load due to the presence of seal, the lack of liquid in a sealed chamber occurred when starting the pump dry friction; b) lower than the saturation vapor pressure of media, making the face film flash occurs, the loss of lubrication; c) If the medium is volatile products, mechanical seal or block the cooling system in the scale, due to end friction and rotating components produce heat leaving the liquid mixing saturated vapor pressure of the medium increased, but also caused the saturation vapor pressure is lower than the media pressure conditions. Due to corrosion caused by the mechanical seal failure a) sealing surface pitting, and even penetration. b) the tungsten carbide and stainless steel seat rings, such as welding, the use of the seat is easy to produce stainless steel intergranular corrosion; c) welded metal bellows, springs and other media in the stress and the common effect of corrosion prone to rupture. Effect due to high temperature mechanical seal failure resulting from a) high temperature thermal cracking is a pump, such as the diesel pump, back to the refinery pumps, atmospheric and vacuum tower bottom pump failure as the most common phenomenon. In the sealing surface at the dry friction, sudden interruption of cooling water, impurities into the sealing surface, taking the time and other circumstances, can lead to radial cracks appeared torus; b) the use of carbonized graphite carbon - graphite ring one of the main seal failure. As the use, if graphite ring once more than the allowable temperature (usually in the -105 ~ 250 ℃), the surface will precipitate resin, friction will occur near the surface carbonized resin, when binder, it will soften the foam, increase the leakage of the sealing surface, seal failure; c) auxiliary seals (such as fluorine rubber, ethylene propylene rubber, all rubber) over allowable temperature, will rapidly aging, cracking, loss of playing hard. Flexible graphite is used in high temperature, good corrosion resistance, but its elasticity poor. And easy to rattle, easily damaged during installation. Seal face wear and tear as a result of seal failure a) friction materials used in poor wear resistance, friction coefficient, end pressure (including the spring pressure) is too large, etc., will shorten the life of mechanical seals. Commonly used materials, arranged by order of resistance: silicon carbide - carbon graphite, carbide - carbon graphite, ceramic - carbon graphite, painting ceramic - carbon graphite, silicon nitride ceramic - carbon graphite, high-speed steel - carbon graphite, surfacing alloy - carbon graphite. b) For solid particles containing medium, the sealing surface into the solid particles is the main reason leading to seal failure. Face of solid particles into the friction from the abrasive effect of intense wear and tear to seal failure. Sealing surface of a reasonable gap, and the extent of the balance of mechanical seals, as well as seal face are caused by film's end flash and other solid particles into the open the main reason for leaving. c) the balance of mechanical seals β also affects the degree of seal wear. Under normal circumstances, a balance of about β = 75% level of the most appropriate. β <75%, although the reduced wear, but the leak increased, increasing the possibility to open the sealing surface. For the high load (high PV value) of the mechanical seal face friction heat as the larger, β generally take 65% to 70% is appropriate for low-boiling hydrocarbon medium, etc., the temperature of the gasification medium is more sensitive, in order to reduce the impact of friction heat, β take 80% to 85% as well. For installation, operation, or the device itself caused the error caused by mechanical seal leakage a) As the installation poor, resulting in mechanical seal leakage. Mainly in the following areas: 1) dynamic and static ring contact surface uneven, bumps during installation, damage; 2) dynamic and static ring ring size is incorrect, damaged, or has not been pressed; 3) dynamic and static ring surface of a foreign body; 4) static and dynamic loading ring against the direction of V-ring, or anti-side installation; 5) leak bushings, seals are not installed or the pressing force is not enough; 6) The spring force is uneven, not vertical single spring, multi spring of varying lengths; 7) The seal chamber face with the vertical axis is not enough; 8) sleeve corrosion on the seal at the point of activity. b) equipment in operation, the mechanical seal leakage, are: 1) The pump impeller axial movement more than the standard, the shaft vibration and periodically unstable process operation, the seal cavity pressure often lead to changes in Dengjun periodic leak sealing; 2) The friction can run together without damage or deformation caused by leakage; 3) the inappropriate choice of seal materials, swelling and loss of elastic; 4) Big Spring turn right; 5) when the vibration is too large equipment operation; 6) dynamic and static ring and the sleeve is formed between the spring scale and can not compensate for loss of elastic sealing surface wear; 7) The sealing ring cracked and so on. c) a period of time after the pump stops when the leak started, mainly because of friction near the solidification of the medium, the crystallization of scale on friction, spring corrosion, obstruction and loss of bombs. d) the shaft deflection is too large. Suggestions High-temperature heavy use of mechanical seal pumps The petrochemical industry, high temperature and heavy use of mechanical seal pumps has been a major problem, such as catalytic cracking oil pump, back to the refinery pumps, bottom pressure pumps, pump IBP bottom, bottom vacuum pumps, radiation delayed coking feed pumps. Heavy medium heat pumps have the following common characteristics: Temperature is high: generally 340 ~ 400 ℃; Medium viscosity: kinematic viscosity in the temperature generally is (12 ~ 180) × 10-6m / s; Medium with particles: such as catalyst, coke, containing sand and other impurities. For the high temperature medium heavy oil pump mechanical seal. Now all companies are using welded metal bellows mechanical seal. Customers are better reflected in Wuhan Degerman PMFL85, PMFL80 type. Bellows material is AM350, INCONEL718, Hastelloy B, C such as stainless steel; corrosion-resistant high temperature alloys, and some wave plate using two-tier structure to make it up to bearing pressure from 2MPa 5MPa, these are an effective solution to the loss of bellows elastic problem. Bellows for coke and coking inside and containing solid particles, etc., the solution has been done on data instructions, such as the use of steam purge, friction with the "hard on hard" with external washing, etc., which in some extent, played a better role, this will not elaborate too much. But then the various methods previously proposed in the practical application of results due to various factors, not ideal. In order to better improve the service life of mechanical seals, joint-owned energy, for a variety of situations, we recommend the following measures should be used together: a) the rotating metal bellows designed structure, rotating bellows mechanical seal with self-cleaning of the centrifugal effect, which can reduce the bellows inside perimeter deposition and coking. b) group of friction materials, we recommend using a "hard on hard" structures, generally tungsten carbide tungsten carbide (including election YG6-YG6) and tungsten carbide on silicon carbide. Use "hard on hard" structure, we must pay attention to the following questions: 1) The cooling system should be protected against interruption of cooling water to prevent the face increased, reduced lubricating film flash seal face lubrication, increased wear and tear; 2) mechanical seal during the installation process, you can top coat to the sealed end of a little cleaning fluids. To prevent the pump from. Seal faces due to lack of lubrication caused by dry friction; 3) Use clean solvent particles outside the washing is to solve the accumulation of more effective methods, but this method the larger waste, and a variety of pump medium, temperature and pressure (fluid pressure than the general requirements of the media side of the high pressure of 0.07 ~ 0.12MPa) and different, more complex structures outside the irrigation system, plus washing facilities outside investment and maintenance costs of consumption, and sometimes cause more harm than good, especially some small and medium enterprises. So many companies abandoned seal oil system, or to not set the system for these cases, it is recommended to use multi-media equipped with isolation seal structure, such as oil pump, back to the refinery pumps, the use of double mechanical seal, between the two seal faces filled with isolation medium (with clean oil, etc.), shown in Figure 3. This structure can effectively extend the service life of mechanical seals, generally up to 6000 ~ 8000h or more. In addition, the use of this consider the following points: ① close to the impeller seal face material selection, a group of "hard on hard" structure (such as YG6-YG6); and close to the mechanical seal gland seal face can use a copper or antimony leaching of carbon - graphite and tungsten carbide or silicon carbide; ② pump used to heat the isolation medium, to have the thermal decomposition temperature, ignition point, high flash point (generally above 260 ℃), thermal oxidation stability, high temperature characteristics of small evaporation loss. Liquid hydrocarbon pump mechanical seal selection Liquid hydrocarbon is a low-temperature liquefied gas medium, with a low boiling point, low viscosity, high vapor pressure and other characteristics. In such conditions the application of mechanical seals, sealing materials will appear brittle cold, atmospheric water vapor atmosphere in the seal on the side of freezing, easily vaporized liquid friction face and so on. Especially when the media a little leak, leakage of liquid hydrocarbon side immediately vaporized in the atmosphere, take away a lot of heat, mechanical seal temperature sharp decline in the use of general sealing materials such as rubber or Teflon generally brittle, resulting in seal failure leakage increases out of control. Some companies use double mechanical seal, in the medium and atmospheric side to set up a quarantine room, during which pass to seal the oil to ease the impact of low temperatures. But this complex structure and systems to be equipped with sealing liquid. From experience, the use of bellows mechanical seal is better, mainly in the use of metal bellows and flexible graphite secondary seal replaced to solve the occurrence of ring material and the cold crisp and loss of elastic buffer issues, such as Wuhan, Degerman PMFL80 type . a) metal bellows material selection, low temperature resistance, good ductility and toughness, Ha-C, AM350, Carpenter20, etc.; b) friction material used in the two special cases: 1) continuous operation of equipment, medium if it contains more of the solid particles, this time using the "hard on hard" structures (in the actual select the YG6-YG6) is better, or more generally continuous operation life of 8000h; 2) intermittent operation of equipment, selection of tungsten carbide or silicon carbide friction of special graphite. c) due to low temperature vaporization of friction face a great influence on the performance of mechanical seals, in addition to select more suitable materials, rational use of end-pressure (mainly the amount of compression of bellows, usually more than usually given in compression volume 15% to 30% is appropriate), in the mechanical sealing elements into the near side of the atmosphere through the cooling water around 25 ℃, in order to improve the environment for Lubrication. Burgmann Sealing Technology, Wuhan 2006-3-24
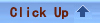 |